Autodesk Technologist with Information about Stormwater Management Model (SWMM) for watershed water quality, hydrology and hydraulics modelers (Note this blog is not associated with the EPA). You will find Blog Posts on the Subjects of SWMM5, ICM SWMM, ICM InfoWorks, InfoSWMM and InfoSewer.
Tuesday, July 30, 2013
Sunday, July 28, 2013
Pump / Force Main System in InfoSWMM and SWMM 5 - with Emojis
Introduction: 💡 The Pump/Force Main system in InfoSWMM and SWMM 5 is a critical component for effective wastewater management. It ensures that wastewater flows smoothly from its source to the desired destination. Let's explore its components and the steps to set it up!
📌 The Basic System:
- Wet Well with its parameters 🕳️
- Pump Type 🔄
- Defined Pump Curve 📈
- Downstream Pressure Node 📍
- Downstream Force Main 🛤️
Step 1: Wet Well Data 📋
- Input the invert elevation and maximum depth of the Wet Well.
- Define the shape, considering evaporation or infiltration factors.
Step 2: Define the Pump Type 🔄
- The pump's operation is guided by its Pump Curve and the set On and Off elevations.
- The four primary pump types include:
- Volume - Flow 🌊
- Depth – Flow 📏
- Head – Flow 📌
- Depth - Flow 📊
Step 3: Define the Pump Curve 📈
- Under the Operation Tab, outline the desired pump curve to ensure efficient pump functioning.
- By setting a positive Surcharge Depth at the Downstream node, you ensure that during the simulation, the node remains pressurized, driving the flow through the Force Main.
- This plot offers a visual representation of the hydraulic gradient line (HGL) for the Force Main System, showcasing the pressure changes within the system.
- Define the downstream conduits emerging from the pump as Force Mains.
- Choose either the Hazen Williams or Darcy-Weisbach coefficient based on your requirements. (This is typically set in SWMM 5 options or InfoSWMM's Run Manager.)
Step 5: Force Main Data 🛤️
Step 7: Pump Summary 📑
- Refer to the RPT File to get a comprehensive summary of the pump's performance and other related parameters.
Conclusion: 🌟 Setting up the Pump/Force Main system in InfoSWMM and SWMM 5 is a meticulous process but ensures efficient and effective wastewater management. Following these steps will ensure a robust system in place! 🚀🌊🛠️
SWMM 5 Pump Curve Head/Flow Curves (1)
Saturday, July 27, 2013
InfoSewer Inflow Control for a Pump with a Pump Curve
Friday, July 26, 2013
Flow Units In InfoSWMM may be different then the Output Link Flow Units
Time Step Selection in InfoSWMM and SWMM5
![]() |
Figure 1: Relationship between the rainfall, hydrology and hydraulic time steps. |
![]() |
Figure 2: Relationship between the minimum, average and maximum simulation time steps and the report time step.
|
InfoSewer Inflow Control for a PUMP
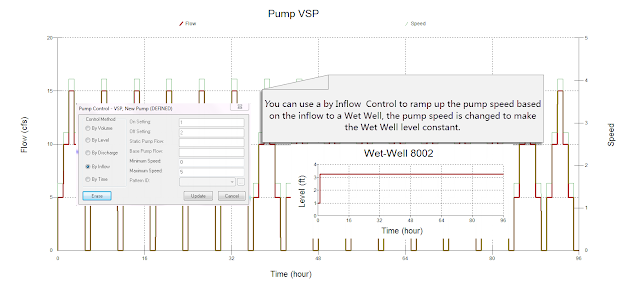
Tuesday, July 23, 2013
Smoother Switching Between Pumps in SWMM 5 - A better simulation of a VSP?
![]() |
Figure 1. Example RTC Rules and VSP Pumps in a SWMM 5 model. |
![]() |
Figure 2. The Pump Curve Used for all 3 Pumps |
![]() |
Figure 3. The Pump Setting for all Three Pumps |
![]() |
Figure 4. Pump Control Curve for Pump 1. The Pump has a Setting of ¼ between 0.5 and 3 feet at the node Wet Well and zero otherwise. |
![]() |
Figure 5. Pump Control Curve for Pump 2. The Pump has a Setting of 1/2 between 3 and 5 feet at the node Wet Well and zero otherwise. |
![]() |
Figure 6. Pump Control Curve for Pump 3. The Pump has a Setting of 1 above 5 feet at the node Wet Well and zero otherwise. |
![]() |
Figure 7. The Flow in all 3 Pumps. |
![]() |
Figure 8. The total flow from all three Pumps to the downstream node. |
Thursday, January 17, 2013
Stopping Tolerance in InfoSWMM, H2OMAP SWMM and SWMM5 Internal Units
InfoSWMM, H2OMAP SWMM and SWMM 5 share the same underlying dynamic engine code but one small difference is that InfoSWMM and H2OMAP SWMM allows the user to select the node stopping tolerance instead of always using the default SWMM 5 stopping tolerance of 0.0005 feet. SWMM 5 uses internal units of feet and shows the output in meters if you are using SI units, as does InfoSWMM and H2OMAP SWMM. The following table shows how the stopping tolerance translates to inches and millimeters in the engine of a US and SI model. The smaller the tolerance the larger the number of iterations used during the simulation but using a very small tolerance does not always mean a better simulation. If possible, for example, with pumps it is better to use a small time step and a medium level tolerance – for example 1 millimeter is a good starting value, but maybe 2 or 3 millimeters may help if you have a continuity error at a pump node.
Stopping Tolerance |
Inches
| Millimeters |
0.1000000
|
1.2000000
|
30.4800000
|
0.0500000
|
0.6000000
|
15.2400000
|
0.0100000
|
0.1200000
|
3.0480000
|
0.0050000
|
0.0600000
|
1.5240000
|
0.0001000
|
0.0012000
|
0.0304800
|
0.0005000
|
0.0060000
|
0.1524000
|
0.0000100
|
0.0001200
|
0.0030480
|
0.0000500
|
0.0006000
|
0.0152400
|
0.0000010
|
0.0000120
|
0.0003048
|
0.0000050
|
0.0000600
|
0.0015240
|
0.0000001
|
0.0000012
|
0.0000305
|
Figure 1 If the node depths between successive iterations are less than the stopping tolerance then the node is considered to be converged. |
AI Rivers of Wisdom about ICM SWMM
Here's the text "Rivers of Wisdom" formatted with one sentence per line: [Verse 1] 🌊 Beneath the ancient oak, where shadows p...
-
@Innovyze User forum where you can ask questions about our Water and Wastewater Products http://t.co/dwgCOo3fSP pic.twitter.com/R0QKG2dv...
-
Subject: Detention Basin Basics in SWMM 5 What are the basic elements of a detention pond in SWMM 5? They are common in our back...
-
Engine Error Number Description ERROR 101: memory allocation error. ...